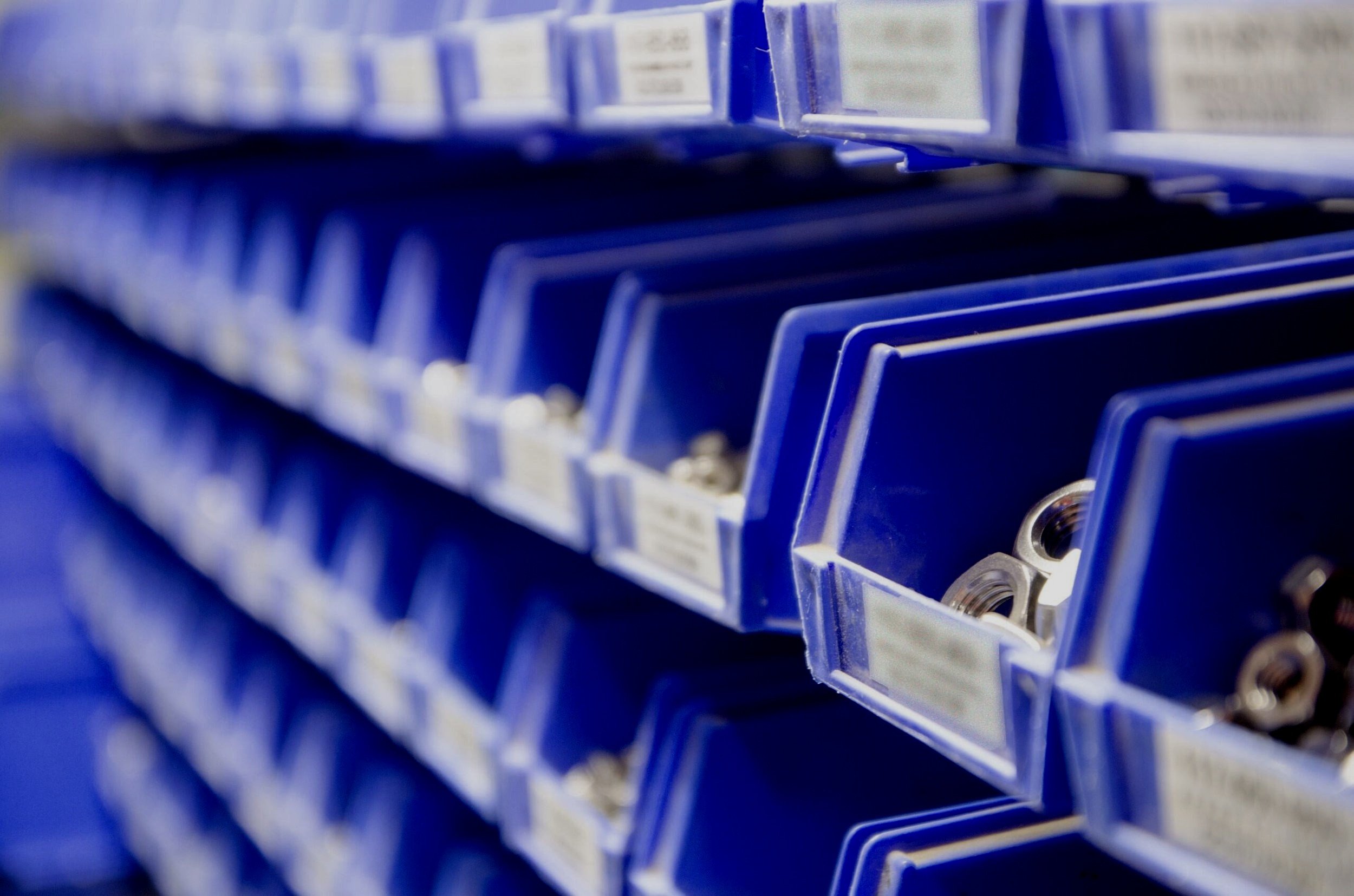
Customized Service Solutions
Enhancing Efficiency with Alloy Fasteners' Customized Inventory Management Programs
Alloy Fasteners offers tailored inventory management programs to enhance efficiency, reduce costs, and streamline manufacturing operations across various industries. These programs provide comprehensive options to meet specific company needs, ensuring optimal inventory control and operational effectiveness. Here’s how Alloy Fasteners' inventory management programs benefit manufacturers:
-
Alloy Fasteners uses fully barcoded systems to ensure precise tracking and record-keeping of stock levels. This accuracy minimizes discrepancies and errors, allowing manufacturers to maintain optimal inventory levels and avoid stockouts or overstock situations.
-
Manufacturers gain operational efficiency through visibility into inventory data via customized reporting features. These reports provide valuable insights into inventory trends, demand patterns, and consumption rates, enabling manufacturers to optimize production schedules, reduce waste, and improve overall resource utilization.
-
Effective inventory management programs lead to significant cost savings by minimizing carrying costs associated with excess inventory and reducing the risk of stock obsolescence. This financial discipline enhances profitability and operational sustainability in competitive markets.
-
Accurate inventory information allows manufacturers to fulfill orders promptly and reliably, improving customer satisfaction by consistently ensuring on-time deliveries and meeting customer expectations. Reliable inventory availability enhances overall service levels and strengthens client relationships.
-
Better inventory control facilitates smoother coordination within the supply chain. Manufacturers can optimize procurement processes, synchronize production schedules, and coordinate logistics more effectively. This streamlined approach ensures the timely availability of materials and components, reducing lead times and enhancing overall supply chain efficiency.
-
Alloy Fasteners' inventory management programs provide valuable insights for forecasting and planning. By analyzing demand patterns and inventory trends, manufacturers can make informed decisions about production volumes, purchasing strategies, and resource allocation, enhancing agility and responsiveness to market fluctuations and customer demands.
Customizable Solutions
-
Bin Stock Programs
Bin stock programs involve strategically placing designated bins stocked with various stainless-steel fasteners at the customer’s facility or job site. Alloy will monitor usage patterns and replenish bins based on predefined stocking levels, ensuring that essential fasteners are always available. This can be a completely hands-off option for our customers.
-
Consignment Programs
Consignment programs involve Alloy placing and managing stainless steel fasteners at the customer’s site. This arrangement eliminates upfront costs for buyers and reduces inventory carrying costs. Manufacturers benefit from having immediate access to various fasteners without the need to maintain extensive inventory levels. It also ensures that essential components are always available, minimizing production delays and downtime. The customer is not billed for the product until it is used.
-
Scheduled Delivers
What should we know about the services you Scheduled deliveries tailored to project timelines and requirements are crucial, where adherence to construction schedules is paramount. Suppliers coordinate with manufacturers to deliver fasteners precisely when needed, optimizing inventory levels and reducing storage space requirements. This just-in-time delivery approach minimizes the risk of stockouts while ensuring operational continuity and cost efficiency.
-
Blanket Orders
Blanket orders allow manufacturers to secure pricing and availability for a predetermined quantity of fasteners over an extended period. This strategic purchasing approach provides stability in pricing, simplifies procurement processes, and ensures consistent supply throughout the project lifecycle. It also enables buyers to negotiate favorable terms and conditions with suppliers, contributing to cost reduction and budget management.
-
Reporting & Inventory Management
Effective reporting and inventory management are facilitated through detailed tracking systems and regular reporting mechanisms provided by suppliers. Your purchasing department will gain insights into fastener usage patterns, inventory levels, and consumption rates, enabling proactive decision-making and efficient resource allocation. Real-time data and analytics empower stakeholders to optimize inventory control strategies, minimize waste, and maximize operational efficiency.
-
Barcoding & Product Consolidation
Barcoding technology enhances inventory accuracy and efficiency by streamlining the identification and tracking of fasteners. Each item is assigned a unique barcode, allowing for automated inventory management, quick replenishment, and accurate order fulfillment. Product consolidation further simplifies logistics by bundling related fasteners into cohesive units, reducing handling costs and improving warehouse space utilization.
-
Technological Integration
Utilizing cloud-based systems and electronic data interchange (EDI) for ordering and invoicing streamlines administrative processes, simplifies workflows, reduces paperwork, and improves processing efficiency. Barcoding capabilities further enhance operational transparency and facilitate seamless inventory management across all stages of production and distribution.
-
Also available:
- Tote Systems
- Screw kitting and assembly services
- Packaging and labeling with barcoding for easy dock-to-stock efficiency
- Full racking and bin set up for optimal efficiency
- Advisory services from experienced personnel to streamline your inventory for fewer skews and increased buying power.
Alloy Fasteners' tailored inventory management programs and services empower manufacturers with the tools and strategies to achieve operational excellence. By improving inventory accuracy, increasing efficiency, reducing costs, and enhancing customer service, these programs enable manufacturers to navigate challenges effectively and capitalize on growth opportunities in dynamic markets.